surfaceone
Well-Known Member
- Joined
- Dec 9, 2008
- Messages
- 11,161
- Reaction score
- 24
- Points
- 0
There was a mold of Binney's DV bronze, one of Binney's 51C iron, one made on Kelley #4 mold iron, one made of Nodular iron, one made of Overmyer's bronze and I would have to get into old notes to find the other metals.Â
Hello RED,
Sounds as if you're at the top of your game, again. I'm very pleased to see you so engaged. You're the only guy I know who can discuss "Malcomized iron cavities."
I'm sorry to say, that all of the above is, I don't even know how many feet, over my head. Metallurgy makes my head swim.
*********
How's your glass chemistry equation working today? [8D] I'm talking 19th Century production, like Lockport, Pittsburgh, Jersey, et al. Were there appreciably different batch glass "formulas" from area to area, for any given color?
Yes I know Lockport made other colors of glass. They also ran a well controlled clean operation because their glass was always good looking stuff.
Why is the Lockport Green so distinctive, compared to other green wares? Their Cobalt is pretty bold, as well. The West Coast guys are deservedly chauvinistic about Pacific Glass Works bottles and their clarity and depth of color. The West coast guys sometimes speak of the sand used as the "Secret ingredient." May some of that sand have been imported?
What about 7 Up green, while we're at it.
Chris got me thinking on this track when he said,
I think another reason why these bottles may not be surviving is the glass chemistry between modern art glass and antique bottle glass. I don't think most modern art glass would be very well suited for mold blowing by hand.
and then he said,
The more I think about what I have read and what I believe I know about 18th and 19th century glass making the more I realize that the picture is very far from complete. Much of the process involved seem to have been lost to history and as such must be reinvented by the modern collector to offer a more complete understanding of how the bottles we collect were manufactured.
The only way to do this is through experimentation based off of physical evidence present on the bottles themselves and through archaelolgy evidence from early glass houses. I think we may all be surprised at how complex the process of making glass and molds and blowing bottles actually is without modern equipment. This is likely why the secret of making glass was closely guarded...
Would the early glass houses have had chemists on staff to adjust the batch? Or would that have been the purview of the chief glassmaker? Would they have used solid moulds like Matt's
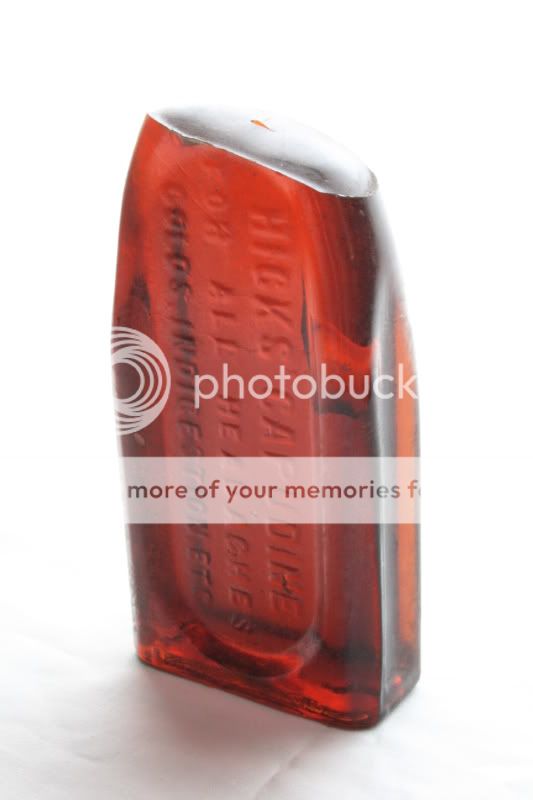
How much of an effect on the bottles would the quality / chemical composition of the sand have had? Was it they key ingredient of Bixby or Ball Blue? Was wood ash critical?
RED, you've forgotten more than I'll ever know about bottle making. Can you shed some light on my poorly asked questions? If, so, please give it the slightly smarter than a 5th Grader treatment. [8D]
We just no longer see the range of color, the thickness of the glass, the remarkable mould making artistry in today's glass objects. We're poorer for it. T'is a wonder to dig or find the mysteriously wonderful glass objects of an earlier time.
